行业新闻
蜂巢能源总裁杨红新:呼吁全行业投入到车规级标准制定中来
2020-01-13 10:53:57
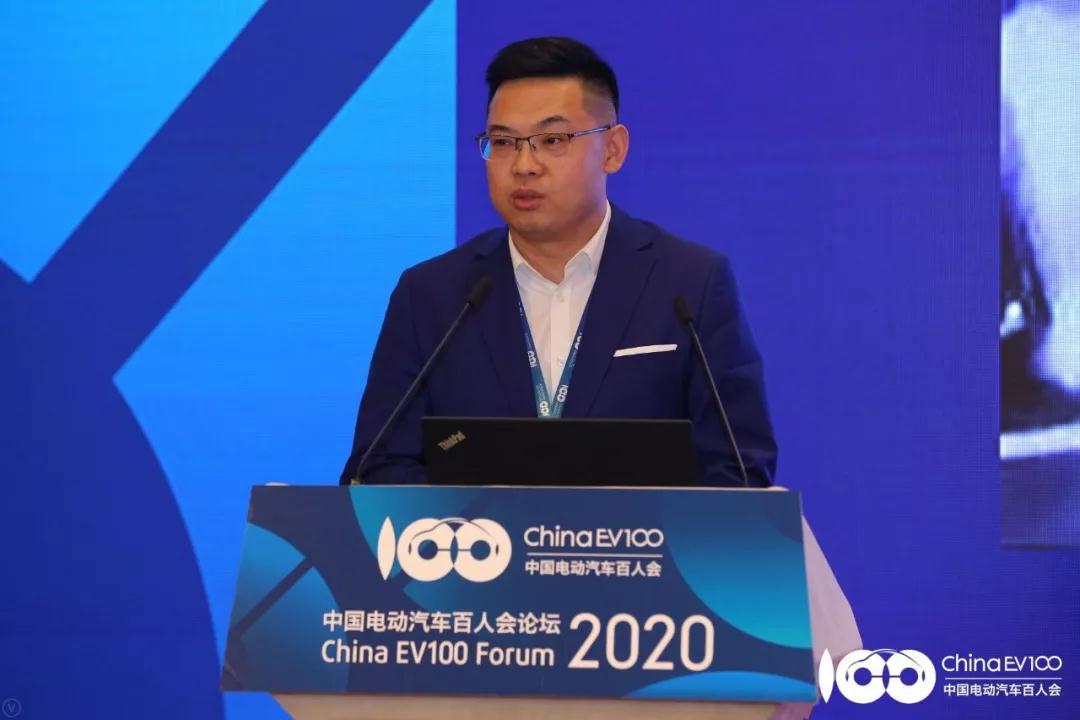
蜂巢能源科技有限公司总裁 杨红新
各位专家,各位嘉宾,大家上午好,非常荣幸跟大家分享。
蜂巢能源是一家年轻的公司,但是还是做了一些比较有特点的事情,代表未来的工作。我们主要的产品是高速叠片的方形动力电池,同时我们打造车规级的标准体系,来制造车规级的产品。车规级的产品目的还是为了解决安全问题,是由于动力电池的使用场景变化而衍生出来的内容,我今天的演讲主要围绕着车规级制造与动力电池安全性的结合进行汇报。
动力电池还是目前安全问题最主要的原因,做电力电池的责任是责无旁贷的,这是必须要解决的问题,解决安全问题从很多方面出发,刚才各位嘉宾报告过的整车层面,系统层面,电芯肯定是最关键的,因为它是热失控的来源,为什么有这么多安全事故,到底问题出在哪里?其中一个主要原因,这是场景的转换带来的一个变化,但是我们没有准备好迎接这个变化。这是传统的锂电池的演变过程,在车上应用以后,对场景提出了新的要求,比如车上使用时间更长,环境更恶劣,低温,高温,雨雪,颠簸路面。另外,手机只有一块电池,但是车上我们至少需要80多块大电池,如果18650,21700,可能需要8、9千支电芯,如果一致性保证不好,会大大影响到整车的可靠性。还有是一致性,电芯的热失控,当然有制造的问题,也离不开原材料的管控,我们原材料控制体系,供应商管理体系,是不是达到了车规级的要求?虽然中国原材料体系在蓬勃的发展,但是我们经过现场的审核,还是有很多问题的,还是不能完全达到车规级的要求。另外制造、控制和工艺管控的进步和迭代,从(原注)到软包,到我们现在使用的方形高速叠片的技术,叠片电池可以带来循环寿命的提升,散热性更好,温升小,能量密度的提升,但是这种新的工艺会伴随着工艺管控环境同步都要提升,也是一个巨大的挑战,所以我们认为这是传统锂电池与车用动力电池一个非常大的差异。
车规级不等于传统锂电池,那么车规级的定义,我们自己也作了一个总结,围绕新能源汽车对于安全性、可靠性、一致性的要求制造的,与车辆属性及使用场景密切相关,并通过专项测试的,涵盖但并不限于满足车规级原材料,车规级制造控制,车规级系统化设计,车规级测试规范等一系列标准的动力锂电池。传统的数码的测试方法和我们车用的测试方法是完全不一样的,它的工况更复杂,也有很多的专属性,目前我们的这些测试方法跟标准还有很多需要进步跟完善的地方。
锂电池的火灾事故很大比例是由制造缺陷引发的,为什么制造缺陷会引发这种不可预知的火灾呢?和动力电池的特性有关系,因为有一些产品在出厂的时候,它的潜在隐藏的问题,质量问题,是不能被检出来的,比如极微小的毛刺,极微小的颗粒物,通过原有的检测技术是不能被检出来的,但是电池经过很长时间使用以后,呼吸膨胀,这个颗粒物和毛刺会刺穿隔膜,引发突然的热失控和短路。所以车规级的制造在这个时候就变得非常的关键,它是提升安全性的必由之路,中国和全世界的动力电池的制造体系必须朝这个方面进行转变。那么蜂巢能源我们在常州建的工厂,就是一个车规级的动力电池工厂,同时我们联合中汽协和中国汽车工程学会,也共同发起了中国车规级标准的倡议。
我们的目标有几个,减少或消除因制程缺陷导致的电池安全事故,提升一致性,降低成本,使之符合车规级的使用要求。包括以下三方面的实施,车规级的管控体系和标准保障产品质量和一致性,用高效智能的设备提高效率,降低成本,用AI技术实现信息化和数字化。
首先第一个方面,从最根本的角度出发,加强环境控制,加强投料控制,比如说整个工厂全都是万级洁净度,局部设备达到了千级,也是全行业最高的标准,我们有两次更衣,两次换鞋,全制程的湿度控制都是低于1%的,包括对滚轧温度都提出了更加严格的控制标准。
异物检出的方法必须要更新,以前小于100微米的颗粒物很难完全被检出来,检出率是很低的,除了传统的检测方法以外,我们用微电流这种漏电检测技术,可以把75微米的颗粒物的检出率大于80%,同时还可以对同异物进行检出。另外是毛刺,以前行业里的标准,毛刺是可以超出隔膜的,但是不能超出太多,我们整个制程的标准,设定的是毛刺不允许超出活性物质料区,不能触碰到隔膜,从而大大提高了安全性。
制程管控标准,我们是6希格玛工厂,从4希格玛提高到了6希格玛。缺陷不良率可以小于3.4PPM,整个工厂全制程的控制因子超过2500个,传统的工厂一般在1500-2000个左右,2500个控制因素可以全面和信息化系统进行对接。
另外,从传统的机、料、法、环、时间,五个维度的控制升级到七个维度的控制,把人以及测试数据也全面与MIS系统进行对接。
高效智能的设备,高压微电路的测试设备,加特征曲线的判断,可以大大提高异物的检出率。装备一致性,我们用了新的AI算法,使得装备一致性可以大幅提高。微电压的漏电检测在后段,可以引入高精度的分拆系统。
另外,高速叠片机的设备提高效率,降低成本,我们第二期将使用0.45秒的高速叠片,这也是全球速度最快的。激光模块,可以大大降低毛刺,虽然会产生金属的熔铸,但是通过我们用等离子风的除尘设备,可以有效降低粉尘跟异物的产生,可以达到每分钟2400片,单线效率可以达到15PPM。
离子风,可以实现千级洁净度,传统的用毛刷刷的方式已经被淘汰了。在叠片对齐度方面,注液时间方面,也都有很大的优化,注液时间我们引入了全国最高效率的超高压注液技术,时间缩短了70%。
另外是大数据跟AI工厂,从六个方面引入了AI的大数据技术,我们和华为有全面战略合作,上周也是在这里跟华为举行了签约仪式,下周跟西门子举行AI工厂的签约仪式,从工艺到质量管控,到制程开发管控,到设备健康管控,到供应链需求管控,到智能园区物流的全面与大数据和AI导入的工作。目前我们常州工厂的一期已经实现了视觉缺陷的AI检测,正在开发向激光焊接,包膜,化成等其他工序的AI自主的智能算法。目标还是想减少人工的干预,提高异常的检出率,缩短异常分析的时间,减少不良品的产出。另外,刚才蔚来的黄总跟我们的想法也是很相似的,工厂未来的大数据,制成过程中的参数将来必须和车辆使用端的参数,以及梯次利用的参数全面进行打通,这样的话在车上做数据健康状态分析的时候,可以与制造过程中的数据进行参比对照,更精确的进行健康状态的预测,这种做法的实现必须依靠于工厂的智能化和大数据,所有数据要上云,采集点足够多,经过自动化智能的处理,我们也在跟华为、西门子在开展合作。
未来一定是通过设备AI智能手段及标准化的管控体系形成一套数字化、信息化可复制的车规级动力工厂标准。
我们还是希望新能源汽车已经在国际上具有优势了,还是希望动力电池也具有全球的引领优势,从什么地方做起?除了原材料,除了设计,除了能量密度,安全以及车规级的制造,车规级的标准,是必须要做,我们有机会和希望在车规级做到国际领先。
这也是我们希望与行业一起来做的,我们发起了行业倡议,希望各位同仁一起努力,实现中国车规级产品全球的引领。
我的汇报就到这里,谢谢大家!